10 Facts About Hangar Construction Cost
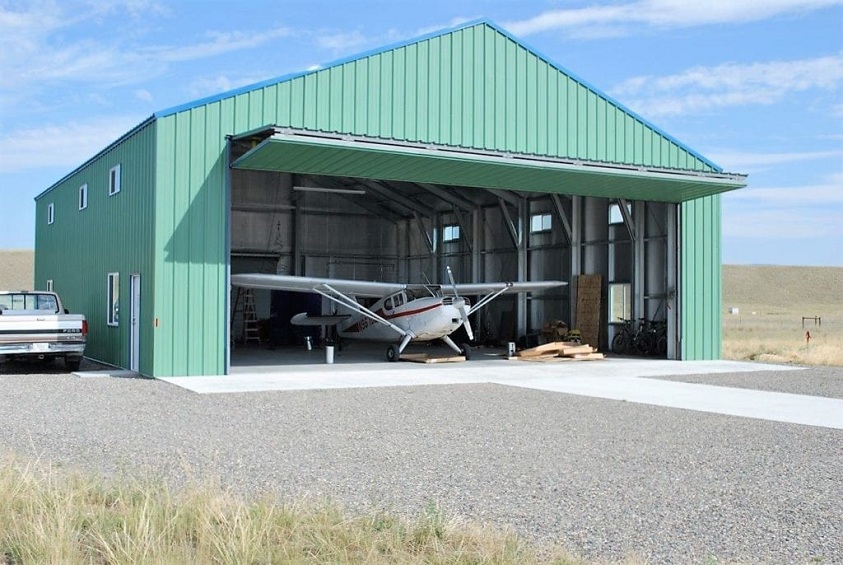
Introduction:
Aircraft hangars are necessities for any major airfield. Hangars provide protection from the elements and can house maintenance personnel, crew, and equipment that may be needed while not in flight. They also provide a place to store aircrafts when they are not currently in use. There are a number of factors can affect the cost of an aircraft hangar construction project. With some planning, you’ll be more prepared to afford this project with just a small budget adjustment or by saving over time for the expenses that will come along with it.
What is Hangar Construction?
Construction of hangars is a time-consuming project and requires skilled labor. Hangar construction often requires specialized concrete, such as high-strength concretes and polymer-modified, which can withstand the weight of the equipment and aircrafts during extreme weather. Most airfields store their aircraft in hangars for maintenance purposes. This is necessary to prevent corrosion from the elements, which could prove very costly in repairs later on. With the proper maintenance, hangars can last for decades without damage so long as they’re well constructed to begin with.
Hangar Construction Cost
The price tag on hangar construction projects are extensive. The cost can vary depending on a number of factors, including difficulty in construction, location of work site and materials used. Other than the materials needed, labor costs may start at $50 per hour and go up from there. Freight costs are also incurred, depending on the location of your project. On average, the total cost for hangar construction can range from $125 to $350 a square foot or higher. For example, a 500-square-foot hangar made mostly of metal may cost about $66,000 dollars to build. The price does not account for engineering fees or travel time for employees. It also does not include government fees that may be necessary in order to obtain permits for construction.
10 Facts About Hangar Construction Cost:
1) Estimating an average hangar costs between $125 and $350 per square foot is a very wide spectrum of costs. As an example, a steel hangar that measures 500 square feet would cost $66,000. The final building can be even more when you factor in engineering fees, materials and travel expenses for construction workers.
2) Hangars are usually constructed off-site by specialized contractors to prevent damaging the buildings near by. This is particularly necessary because there are strict rules about how close construction companies can work to other buildings so as not to impact flight operations at the airfield.
3) Construction companies estimate that it takes approximately 30 days of labor to construct a double-walled aircraft hangar from start to finish at an airfield. This does not include time for shipping materials to the work site.
4) A variety of different factors can impact the cost of building an aircraft hangar. The materials used and the location of construction are two examples of this.
5) The price of constructing a hangar also depends on who will be paying for it. For example, if you are funding it yourself, your costs will be much higher than if you were getting a loan for material costs, labor and engineering fees.
6) Unlike with other construction projects, hangar projects have strict regulations in place so as not to disrupt flight operations at your local airfield. Hangar buildings must be constructed at least 10 feet away from any runway, taxiways or apron. The hangars are also required to be built at least 100 feet away from any building used for the purpose of storing or repairing military equipment or aircrafts.
7) The construction of aircraft hangars can take thousands of man hours to complete due to the amount of materials and the amount of skilled labor needed for their construction. On average, it takes approximately 30 days for a hangar to be constructed on site and that does not include time needed for shipping materials. 8) Hangar construction may also require specialized concrete that can withstand the weight of the aircraft and all its equipment during extreme weather conditions.
8) Hangar structures are often built with concrete, which makes it necessary for special tools and equipment to do the job. Most of these tools are rented out so that they can be used on other projects after they’re returned. If you have to purchase the tools, it could increase your costs considerably.
9) If you don’t intend to use the hangar after its completion, the construction company might give you a discount in your final price. You could also choose to build it for someone else and earn a profit instead of paying for it out of pocket.
10) The construction of hangars is a time-consuming project that requires skilled labor and materials that can stand up to extreme weather conditions.
Conclusion:
Hangar construction can be a very expensive venture, but the most important thing to remember is that it’s necessary. If you’re piloting planes or keeping them in good condition, you’ll need to know how to build a hangar and what materials are needed so you can budget accordingly.
Whether you’re planning on building your own hangar or purchasing one, this guide will get you headed in the right direction as far as building goes. With useful information from experts, we hope that this article was helpful for anyone seeking more information about hangars and hangar construction costs.